Recognizing What is Porosity in Welding: Causes and Solutions
Recognizing What is Porosity in Welding: Causes and Solutions
Blog Article
The Scientific Research Behind Porosity: A Comprehensive Overview for Welders and Fabricators
Recognizing the complex mechanisms behind porosity in welding is critical for welders and fabricators making every effort for impressive workmanship. From the make-up of the base products to the complexities of the welding procedure itself, a wide variety of variables conspire to either aggravate or relieve the presence of porosity.
Recognizing Porosity in Welding
FIRST SENTENCE:
Assessment of porosity in welding exposes important understandings right into the stability and quality of the weld joint. Porosity, characterized by the visibility of dental caries or spaces within the weld steel, is an usual problem in welding processes. These spaces, otherwise properly attended to, can endanger the structural integrity and mechanical buildings of the weld, resulting in prospective failings in the ended up product.
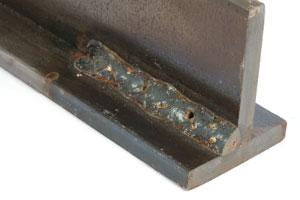
To detect and evaluate porosity, non-destructive testing techniques such as ultrasonic testing or X-ray inspection are frequently employed. These strategies permit the identification of internal issues without jeopardizing the stability of the weld. By evaluating the dimension, shape, and distribution of porosity within a weld, welders can make educated choices to boost their welding procedures and accomplish sounder weld joints.

Variables Influencing Porosity Formation
The event of porosity in welding is affected by a myriad of elements, varying from gas shielding performance to the ins and outs of welding parameter setups. One critical factor adding to porosity formation is poor gas shielding. When the protecting gas, generally argon or carbon dioxide, is not successfully covering the weld pool, climatic gases like oxygen and nitrogen can contaminate the liquified metal, causing porosity. In addition, the tidiness of the base materials plays a considerable function. Contaminants such as rust, oil, or moisture can evaporate throughout welding, developing gas pockets within the weld. Welding criteria, consisting of voltage, existing, take a trip rate, and electrode type, likewise impact porosity development. Utilizing inappropriate setups can generate extreme spatter or warmth input, which subsequently can result in porosity. In addition, the welding strategy utilized, such as gas metal arc welding (GMAW) or protected steel arc welding (SMAW), can influence porosity formation because of variants in warm distribution and gas protection. Understanding and regulating these elements are crucial for reducing porosity in welding procedures.
Effects of Porosity on Weld Top Quality
The existence of porosity likewise deteriorates the weld's resistance to rust, as the entraped air or gases within the voids can respond with the surrounding setting, leading to destruction over time. In addition, porosity can prevent the weld's capacity to withstand stress or impact, more endangering the general quality and reliability of the welded structure. In vital applications such as click aerospace, automotive, or structural buildings, where safety and security and longevity are critical, special info the damaging effects of porosity on weld high quality can have severe effects, stressing the value of reducing porosity through correct welding strategies and procedures.
Strategies to Minimize Porosity
In addition, making use of the ideal welding criteria, such as the proper voltage, existing, and take a trip speed, is vital in preventing porosity. Maintaining a consistent arc size and angle during welding likewise assists lower the probability of porosity.

Furthermore, choosing the ideal securing gas and preserving correct gas circulation rates are vital in lessening porosity. Using the suitable welding technique, such as back-stepping or using a weaving motion, can likewise assist disperse heat evenly and minimize the chances of porosity development. Guaranteeing proper air flow in the welding atmosphere to get rid of any kind of potential sources of contamination is crucial for achieving porosity-free welds. By executing these methods, welders can efficiently minimize porosity and produce premium welded joints.

Advanced Solutions for Porosity Control
Carrying out sophisticated modern technologies and cutting-edge find out this here methods plays a crucial duty in achieving superior control over porosity in welding procedures. In addition, utilizing advanced welding techniques such as pulsed MIG welding or customized environment welding can additionally help reduce porosity problems.
One more innovative service entails the usage of innovative welding equipment. Making use of tools with integrated attributes like waveform control and sophisticated power sources can improve weld top quality and lower porosity risks. The application of automated welding systems with accurate control over parameters can considerably lessen porosity issues.
Furthermore, integrating sophisticated tracking and evaluation modern technologies such as real-time X-ray imaging or automated ultrasonic testing can assist in detecting porosity early in the welding process, enabling for instant restorative activities. In general, incorporating these sophisticated services can considerably enhance porosity control and boost the overall top quality of welded components.
Verdict
In conclusion, recognizing the scientific research behind porosity in welding is vital for welders and makers to produce high-quality welds - What is Porosity. Advanced remedies for porosity control can further enhance the welding process and guarantee a strong and trusted weld.
Report this page